Authored by Susan Cheah
Published at 06 May, 2021
The Process of Recycling Used Cooking Oil
Our planet population has been on the rise in the last few decades. It has then led to a surge in the consumption of food. This has also indirectly led to a huge amount of used cooking oil (also known as waste cooking oil) in the process of preparing the food.
Basically, used cooking oil is generated from the cooking process for human daily consumption. Its source may be derived from households and commercial activities. Due to its chemical features, recycling of used cooking oil not only provides a renewable feedstock for producing biofuels like biodiesel and various biobased products but also mitigates greenhouse gas (GHG) emissions and avoids environmental pollution arising from its improper handling (e.g., disposed of at kitchen sink or drainage).
Thankfully, thanks to the sufficient awareness campaign by our local governments, and even more importantly, the economic factor resulted from the increasing demand for waste oil globally. Recycling of used cooking oil has been gaining traction among operators in the foodservice industry like restaurants & hotels.
Once the used cooking oil is being collected and send to recycling facilities by professionals like Capital Oil, these oils are that being treated with various processes to give it a second life.
Removing Water
The first step typically involves removing any water within the oil. Water found in used cooking oil is either free water or bound water. Dewatering is usually referring to the processing of removing the free water. In cases where water has been emulsified with oil, a demulsifier has to be used to break up the emulsification before the water can be removed with dewatering.
Dewatering is a simpler process relying on the separation of aqueous and oil phases under the influence of gravity. One of the techniques to achieve this is to place the oil in a large tank, to let it set over a period of time, which will separate the oil and water.
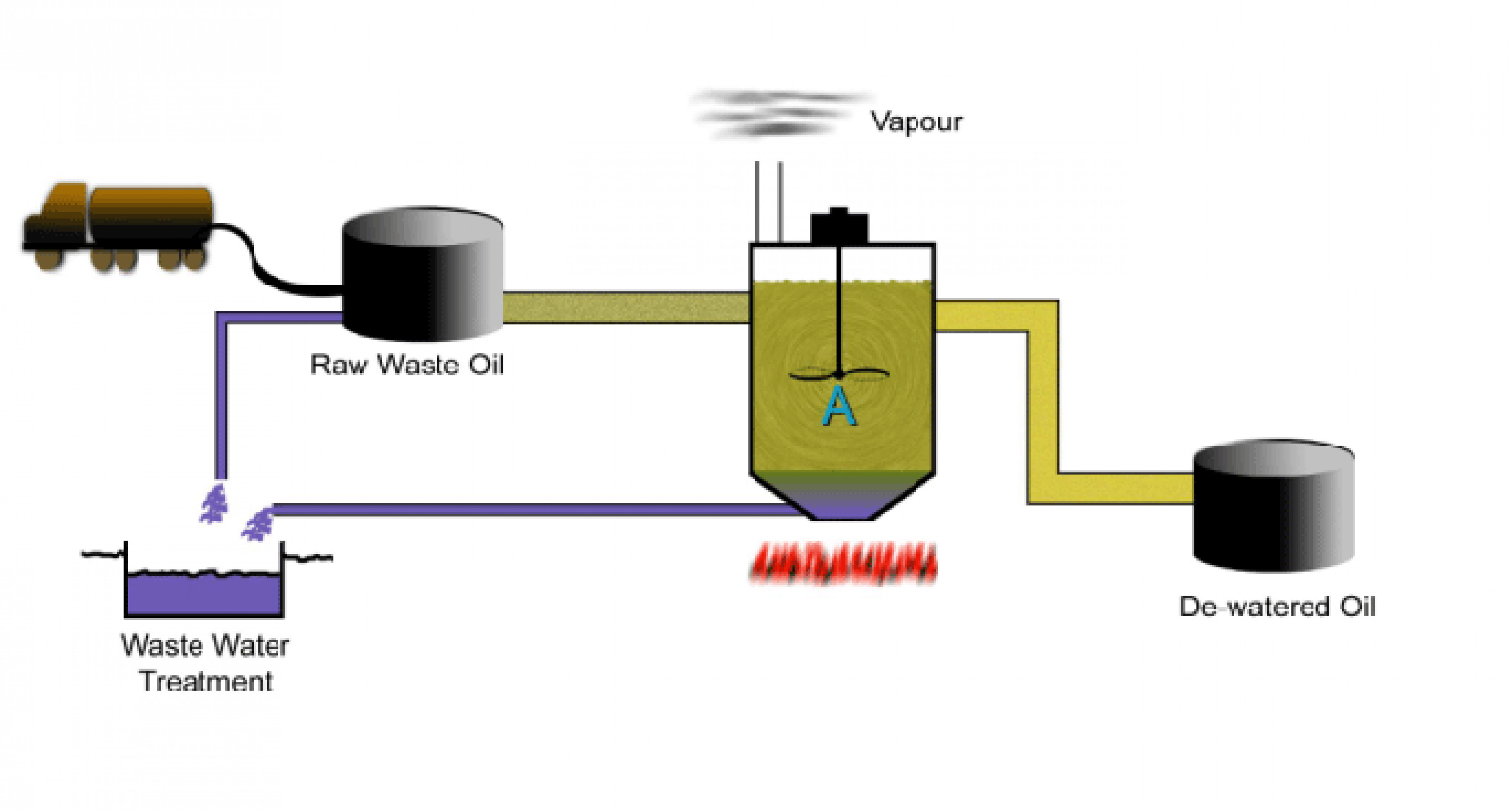
To speed up the process of dewatering, the oil in the tank can also be heated and stirred to drive off the water through evaporation.
The out of is a dried or dehydrated oil that is ready for further processing or ready to be used as burner fuel.
Filtering & Demineralisation
Next in the process is to attempt to remove inorganic materials and undesired additives from the used cooking oil to produce a cleaner fuel or to be the feed for re-refining.
To do this, used cooking oil feedstock is being transferred to a reaction tank to mix with a small quantity of sulphuric acid and get heated. A chemical surface-active reagent, known as a surfactant, is then added and after stirring, the mixture is allowed to stand. This separates the mixture into two “phases”, the oil and water-based.
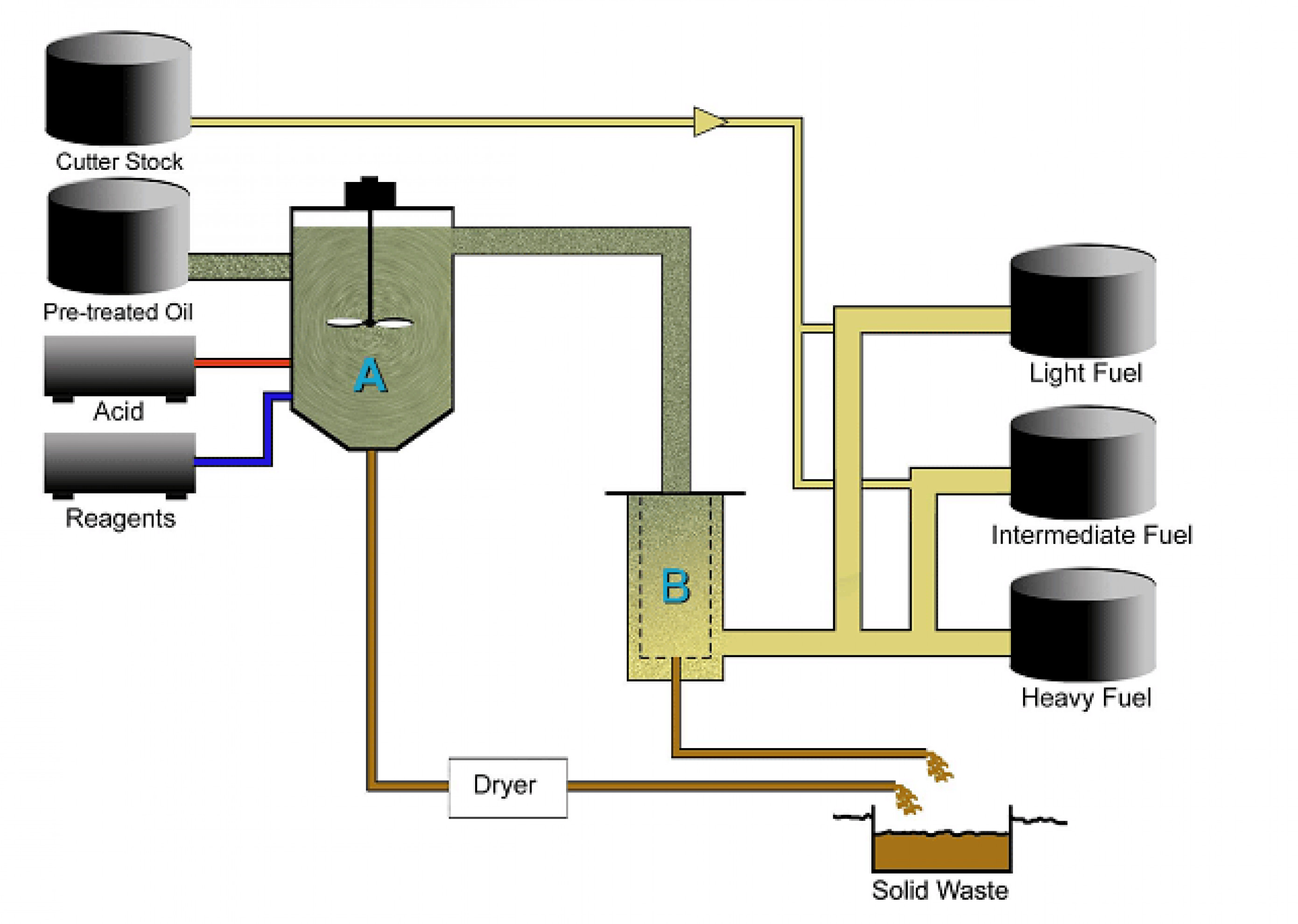
The reagent resulted in the contaminants accumulating in the water-based phase, which will settle to the bottom of the tank, which is then drained off as slurry. This phase contains acid, used oil contaminants, like metals and some other additives. The solid waste left over after the water is dried off will be disposed of carefully.
The now demineralized oil is then simply filtered to remove suspended particles and being stored as clean burner fuel. The same fuel if needed can further be diluted with a lighter petroleum product - the cutter stock to produce various light fuel oils depending on the fuel viscosity requirements of the burner.
Propane De-asphalting
Further down the process, the clean burner fuel can be used to produce de-asphalted lube-oil with a process known as the propane de-asphalting (PDA). The de-asphalted lube-oil can then becomes the feedstock for the next step in the re-refining facility.
The propane de-asphalting process relies on the greater solubility of the paraffinic and naphthenic components versus the contaminated waste material in a stream of propane.
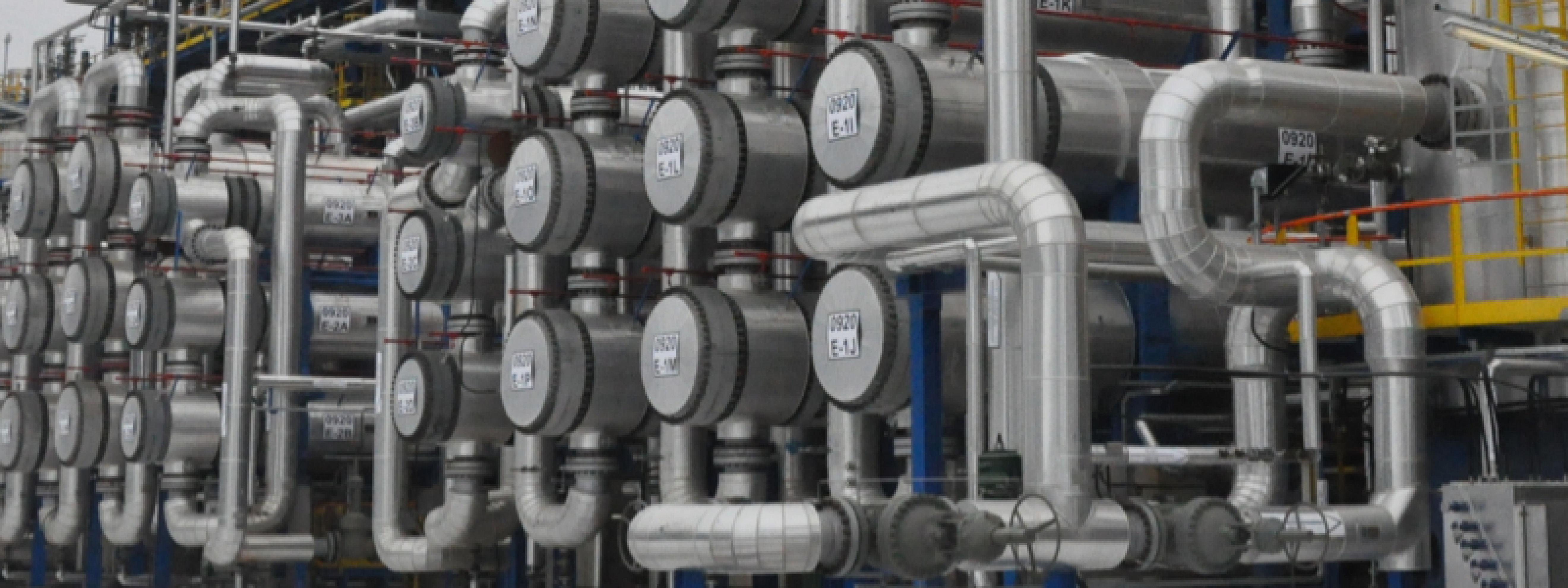
The used cooking oil is pumped into the middle of an extraction column where liquid propane is charged to the bottom of the column the same. The oil being heavier than propane will flow down the column. The propane rises in a counter-flow thus mixing the input streams. The rising propane will dissolve the more soluble lube oil components, and the propane insoluble material is removed from the bottom of the column.
Propane will then be vaporized in a stripper unit, which will then be condensed and returned to the propane storage tank for reuse, whereas the de-asphalted lube-oil component will be feed for the next stage of processing.
Distillation
The core process for re-refining is distillation also known as fractionation. The process separates the component of lubricating oil physically by boiling range. The boiling ranges can produce gases and gasoline at the lower boiling points with heavy lubricating oils being distilled at higher boiling points depending on the type of distillation.
Conclusion
Used cooking oils (UCO) represent a valuable source of raw materials with a wide range of applications, from energy to lubricants or bioproducts. Due to their waste-nature and huge and diffused availability in recent decades, used cooking oil fit well in the circular economy model, causing great interest for their integration into various existing processes and also the development of new sustainable productions.
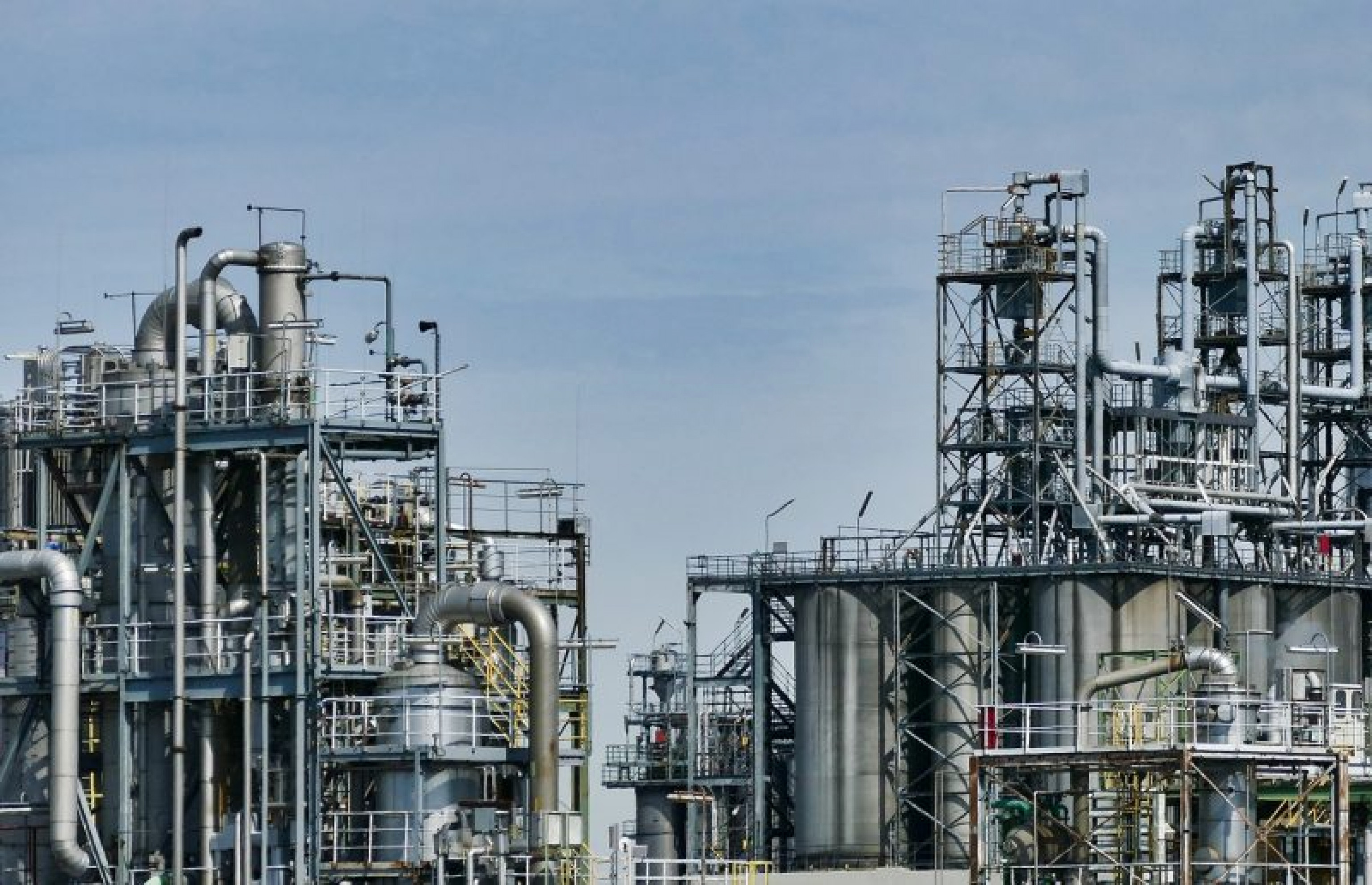
In recent years, advancements in technology, both in terms of processes and materials involved in the process enabled the recycling of used cooking oil to be even more efficient and sustainable. Mini plants designed for fast physical treatment of waste oils are also available on the market. Looking at the future, the integration between academic and industrial research activities will be fundamental in order to develop recycling treatments that are truly able to substitute existing productions, which involve non-waste raw materials.
If you are running a commercial kitchen or in the foodservice industry, you can be a part of this good simply by recycling your used cooking oil with us. Capital Oil offers a quick, clean, and timely collection of Used Cooking Oil (UCO). Collection schedules are established in advance with customers to ensure there are no overflows of UCO and are generally scheduled on a weekly service cycle. We can also customize a collection interval to suit your specific needs.